BlueLine parallel bur – bredent launches innovative tool onto the market
- Innovative approaches to solving problems when post-machining CNC-milled telescopic crowns or bars by hand.
- Overview of the advantages of bredent parallel burs – insights from practice.
- Facts and details on technical implementation.
Dental laboratories need to rework CNC-milled telescopic crowns or bars by hand. Metals such as CoCr and titanium differ from cast alloys in terms of their properties in their raw form. As a result, manual post-machining with conventional tools is difficult to achieve a smooth surface in a short time.
bredent offers innovative approaches
The BlueLine parallel burs are adapted to the mechanical properties of CoCr and titanium metals. The specially developed toothing ensures effective manual post-machining. These tools are available in two versions: for use in milling machines up to 30,000 rpm (range REF 33000839) and for high-frequency milling machines up to 60,000 rpm (range 33000841). The set includes four tools, covering the range from super coarse to high-gloss processing. All tools can also be purchased separately.
BlueLine parallel burs up to 30,000 rpm are equipped with the time-tested Diatit surface treatment. The BlueLine HF parallel burs up to 60,000 rpm are not surface-hardened.
Master dental technician and laboratory owner Josef Miller: “The uncoated BlueLine HF parallel burs are particularly impressive for non-precious metals at a milling speed of 50,000 revolutions. As far as I’m concerned, there is no better product on the market. We’re able to observe a time saving of up to 50 percent in our lab.”
The BlueLine parallel bur
The combination between the high number of cutting edges and a flat twist angle* produces a high removal rate with extremely smooth running. This smooth running prevents chatter marks on the work piece, creating a high-gloss surface from the outset; post-machining is no longer necessary.
The burs also feature a Diatit surface treatment, which also helps to ensure smooth running and provide a high-gloss surface. The Diatit surface treatment also results in increased tool hardness, thus guaranteeing a long service life.
Conventional milling tools have a steeper twist angle*, leading to chatter marks, which require extensive post-machining.
The BlueLine high-frequency parallel bur
Conventional milling spindles operate at up to 30,000 rpm. However, increasingly more laboratories are using a conversion kit on their milling machine to provide a high-frequency milling spindle that operates at up to 60,000 rpm.
The special BlueLine HF bur set (HF = high frequency) with a special cutting edge geometry has been developed for these high-frequency milling spindles. This high speed bur set creates high surface qualities and a completely smooth surface, which is particularly important for the precision required for CAD/CAM work.
A Diatit surface treatment would not produce an optimal surface at these speeds and is therefore not used.
Master dental technician and laboratory owner Claus Küchler (developer of the Telemaster system) assisted bredent during the development phase of new parallel burs for telescopic technology. After a year of testing, the results were conclusive: “We use non-precious metals almost exclusively as the material for our telescopic technology and work with a milling machine at 50,000 rpm. It became evident that bredent’s new burs cut exceptionally fast with a smooth surface and low thermal variation. The very long service life is also worth mentioning. Our verdict: excellent everyday usability, parallel burs with a long service life.”
Facts and details on technical implementation
Tool length: 34 mm
Length of working part: 11 mm
Shaft diameter: 2.35 mm
Diameter of working part: 2 mm
Radius: 1 mm
Application: BlueLine up to 30,000 rpm (ideal working speed: 20,000 rpm)
BlueLine HF up to 60,000 rpm (ideal working speed: 50,000 rpm)
CoCr (BlueLine HF)
CoCr and titanium (BlueLine)
Surface: BlueLine: Diatit surface treatment
BlueLine HF: no remuneration
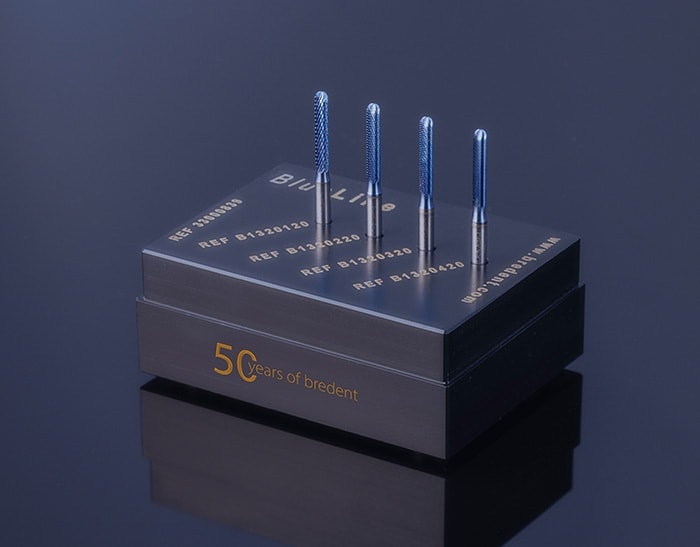
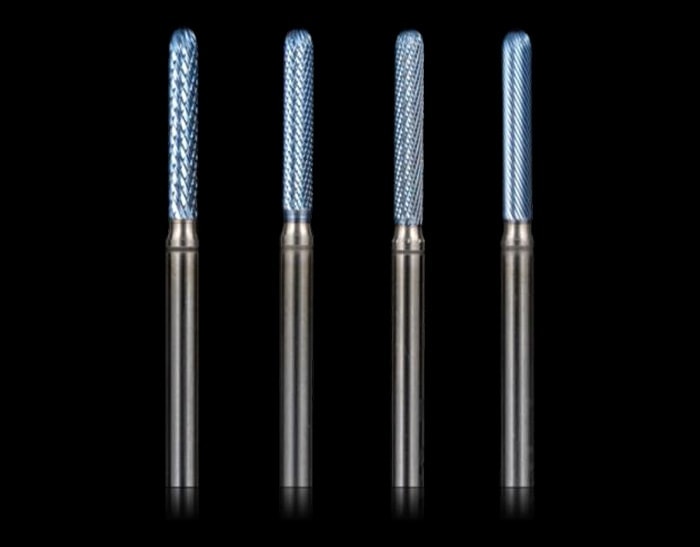
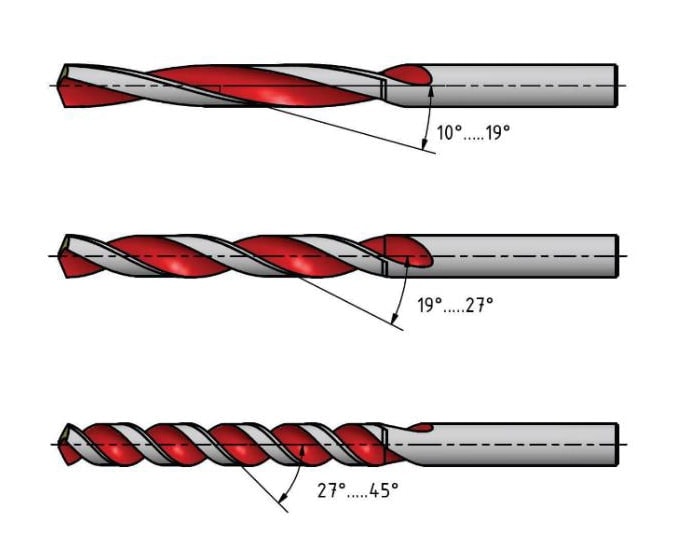
stay tuned
Subscribe to our bredent group Press Mailing List